Toyota Suivi de Commande
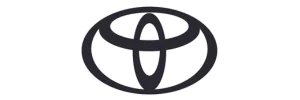
Entrez votre numéro de suivi et cliquez sur le bouton
Consultez l’état de votre livraison Toyota Suivi de Commande et anticipez sa disponibilité au point de retrait.
Coordonnées
- Numéro de téléphone: +33 (0)1 47 10 81 00
- Adresse de l’entreprise: 20 Boulevard de la République, 92420 Vaucresson, France
- Lien du site web principal: https://www.toyota.fr/
- Suivre également: Linehaul Suivi Colis
Optimisation Logistique
Cette organisation utilise des outils numériques pour structurer l’ensemble de son réseau d’approvisionnement. Elle analyse les flux internes afin de réduire les distances inutiles dans les chaînes de transport. Elle sélectionne des logiciels capables de calculer, à partir de volumes, les itinéraires les plus efficients. Chaque outil propose une visualisation de données facilitant les décisions liées aux ressources matérielles.
Les équipes intègrent ces fonctions dans leur système de gestion pour aligner les données terrain avec les prévisions de production. Les résultats permettent d’éviter les surstocks et de minimiser les mouvements répétitifs entre entrepôts. L’outil guide également les ajustements en cas de changement dans la demande régionale. La direction du réseau intègre cette solution dans les processus d’amélioration continue. Les modules numériques offrent ainsi une meilleure lecture de la complexité logistique sur le plan opérationnel.
Intégration Système
Les responsables intègrent des applications internes capables de synchroniser les informations entre les unités de production. Ils privilégient les interfaces simples qui dialoguent avec les plateformes industrielles existantes. Les systèmes connectent les données liées aux pièces, aux délais, et aux destinations finales. Cela permet d’automatiser certaines étapes du traitement logistique sans intervention manuelle.
Les mises à jour en temps réel évitent les écarts de stock et les retards de livraison. Les employés consultent les mêmes référentiels, ce qui garantit l’unicité de la donnée. Des règles automatiques orientent les décisions dès qu’une anomalie est détectée dans les délais prévisionnels. Les interfaces fonctionnent sur plusieurs niveaux et s’adaptent aux évolutions sans nécessiter de recodage fréquent. Chaque composant est pensé pour évoluer en fonction du volume ou de la complexité croissante du réseau industriel.
Numérisation Industrielle
Les équipes mettent en place des guides numériques pour standardiser les procédures internes. Elles utilisent des tablettes et écrans mobiles afin de transmettre des consignes opérationnelles. Ces supports remplacent les instructions papier, améliorant ainsi la réactivité sur les lignes de montage. La précision augmente grâce à l’accompagnement visuel dans le montage de composants ou d’accessoires.
Le personnel gagne en autonomie et réduit les temps de formation. Les responsables évaluent régulièrement les bénéfices de ces pratiques via des retours d’expérience. Chaque poste adapte ses flux en fonction des consignes reçues numériquement. La transition se déroule progressivement pour maintenir la continuité des activités. Les logiciels accompagnent également le suivi qualité sans recourir à des contrôles systématiques hors ligne. L’entreprise structure ainsi un environnement d’exécution appuyé sur des outils dynamiques.
Coordination Réseau
L’ensemble du réseau logistique adopte une planification basée sur les délais réels et non estimés. Les centres de distribution définissent les priorités en fonction des engagements pris sur le terrain. Chaque livraison s’appuie sur des données validées plutôt que sur des historiques peu représentatifs. Les outils informatiques transmettent ces délais confirmés aux entités concernées pour adapter la production.
La priorité est donnée aux produits selon leur rotation, leur rareté ou les contraintes contractuelles. L’analyse de charge par région améliore la fluidité des opérations. Le réseau fonctionne sur une logique de flux tiré, piloté par la demande réelle. Cela réduit les stocks dormants et les transbordements non essentiels. Le processus contribue à une meilleure maîtrise des coûts logistiques et une plus grande transparence sur les prévisions.
Agrégation Données
Les plateformes développées rassemblent des informations issues de différents transporteurs ou sous-traitants. Les données logistiques s’organisent en tableaux dynamiques alimentés automatiquement par plusieurs sources. L’utilisateur accède à une synthèse des mouvements, statuts ou écarts sans devoir changer d’environnement. L’intégration se fait via API ou interfaces sécurisées selon la nature des partenaires.
Chaque événement est horodaté et inscrit dans un registre consultable. Les alertes se déclenchent selon des règles prédéfinies par les équipes de gestion. Les anomalies apparaissent sous forme de codes standardisés, compréhensibles par tous les services concernés. Les rapports générés alimentent les décisions stratégiques en logistique ou en maintenance. Ce traitement centralisé permet aussi de visualiser les performances des acteurs externes. L’entreprise agit alors comme centre d’analyse plutôt que comme transporteur.
Partenariats Techniques
Les projets incluent des coopérations avec des éditeurs de logiciels spécialisés dans la planification industrielle. Les équipes IT collaborent avec des consultants externes pour paramétrer les modules selon les besoins réels. Ces outils orientent les décisions vers des modèles prédictifs, en lien avec les objectifs environnementaux. Certains projets visent à réduire les émissions associées au transport interne.
D’autres se concentrent sur la réduction des délais entre la commande et la livraison client. La mise en œuvre implique souvent une phase pilote avant déploiement complet. Les résultats sont analysés puis partagés entre sites industriels concernés. Ce type d’alliance technique illustre une approche orientée sur la donnée plutôt que sur le volume transporté. Les apports logiciels viennent compléter les moyens logistiques existants sans les remplacer.